Electrospray
Thin Film Deposition of Macro-Molecular Materials Under Ambient Pressure:
Macro-molecular materials have become a major
focus of research in recent decades. This is motivated by the promise
of device applications such as plastic electronics, displays based
on organic light emitting diodes, bio-sensors, or surface coating
uses like controlled drug release, corrosion protection, anti-fouling
coatings, or anti-static protection. Many of these applications are
based on the deposition of well-defined thin film structures of macro-molecular
materials on a wide range of substrates. Since macro-molecular materials
are usually best processed from solution, preparative techniques
such as spin coating, spraying, dipping or ink-jet printing are currently
popular for thin film preparation.
Electrospray combines the advantages
of spray processing (fast, roll-to-roll capable, continuous) with
an expanded parameter space due to electrostatic phenomena. This
can be used to influence the structure of the deposited thin films.
For example, Coulomb repulsion of solute ions during the spray process
strongly influences the thin film structure. Hence, modification
of the solvent environment can be used to achieve specific morphology
goals.
While electrospray has been thoroughly investigated
as a technique for the introduction of ionized large molecules into
vacuum for mass-spectrometry applications (electrospray ionization
mass spectrometry (ESI-MS)), its use as a thin film deposition technique
is a relatively unexplored territory. Our efforts currently focus
on the investigation of the interplay between solution parameters
(composition, concentration, solutes, solvent type etc...), spray
parameters (electrical field, distance, flow rate etc...) and resulting
thin film morphology. Fig.1 shows a schematic of the electrospray
deposition process (see caption for details). Fig.2 shows a photograph
of the electrospray plume during operation.
As an example for various morphologies that
can be produced by electrospray by variation of spray parameters
Fig.3 shows a series of scanning electron microscopy (SEM) images
taken on polylactic acid thin films prepared from dichloromethane
solution at various concentrations but otherwise constant parameters.
The morphology of the films ranges from strongly clustered (right)
to flat thin films (left) as the concentration is reduced from 20
mg/ml to 0.5 mg/ml. Our group is currently investigating the electrospray
deposition of materials ranging from various bio-molecules to polyelectrolytes
and nanoparticles. |
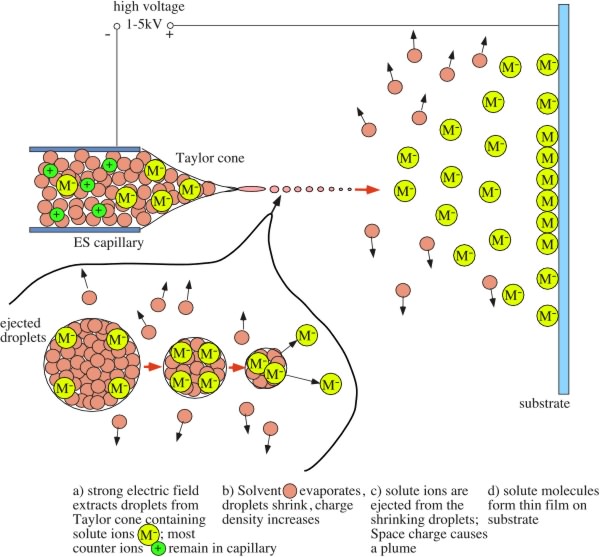
Fig.1: Electrospray deposition process: Solution
is fed through a capillary, which is positioned about 2-4 cm in front
of the substrate. A high voltage applied between capillary and sample
results in the formation of a Taylor cone, where a separation of
positive and negative ions occurs. Droplets containing solvent and
mainly ions of bias-matched polarity are emitted. As the solvent
evaporates the charge density on the droplets increases, causing
droplet splitting and ion ejection. Repulsive forces between the
ions and droplets cause the formation of a wide plume. Once the sprayed
material hits the sample surface a film is formed and charge neutralization
occurs.
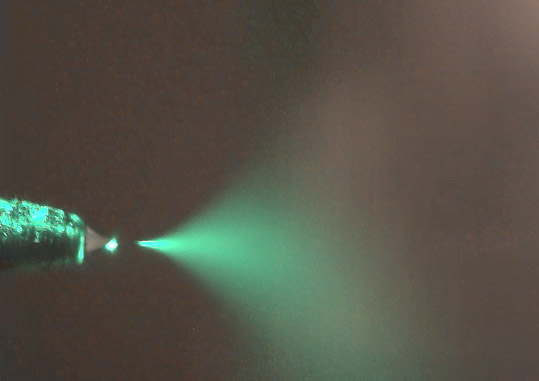
Fig.2: Electrospray plume illuminated with a
green laser. Space charge widens the electrospray to a plume (substrate
is out of focus). |